Analyse technique des solutions pour prolonger la durée de vie des rotors principaux d’hélicoptères : matériaux, maintenance, capteurs et enjeux économiques.
Un enjeu critique pour l’exploitation des hélicoptères
Les rotors principaux sont au cœur de la mécanique du vol en hélicoptère. Ils assurent la portance, la manœuvrabilité et la stabilité de l’appareil. Leur défaillance n’est pas une option, leur entretien est complexe, et leur remplacement coûteux. Prolonger leur durée de vie n’est donc pas un simple défi technique : c’est une nécessité opérationnelle et économique.
Un rotor principal est soumis à des contraintes extrêmes. Il tourne à haute fréquence (300 à 500 tr/min), supporte des charges dynamiques variables, des vibrations importantes, et des variations thermiques rapides. La fatigue des matériaux, l’érosion des bords d’attaque, les microfissures internes et la corrosion sont des facteurs qui limitent sa longévité.
Actuellement, la durée de vie certifiée d’un rotor principal varie entre 2000 et 5000 heures de vol, selon le modèle. Son remplacement peut coûter entre 250 000 et 2 millions d’euros, selon l’hélicoptère concerné. Réduire les cycles de maintenance lourde, anticiper les défauts avant rupture, et optimiser la résistance mécanique sont des objectifs critiques pour les opérateurs civils et militaires.
Cet article détaille les principales pistes industrielles et technologiques utilisées aujourd’hui pour augmenter la durée de vie des rotors principaux, en croisant les approches matériaux, surveillance numérique et conception.
Une évolution des matériaux pour renforcer la résistance à la fatigue
L’un des leviers techniques majeurs pour améliorer la durabilité des rotors principaux réside dans le choix des matériaux. Traditionnellement construits en aluminium ou en titane, les rotors modernes intègrent désormais massivement des matériaux composites, notamment les fibres de carbone et de verre associées à des matrices époxy ou phénoliques.
Ces composites permettent une réduction significative du poids, tout en offrant une résistance à la fatigue 5 à 7 fois supérieure aux alliages métalliques classiques. Ils absorbent mieux les vibrations et supportent davantage de cycles mécaniques sans rupture. Sur les modèles comme le H145 d’Airbus ou l’AW169 de Leonardo, les pales principales sont entièrement en composite et ne nécessitent plus de longerons métalliques internes.
Les avancées récentes portent également sur l’intégration de revêtements nanostructurés sur les bords d’attaque. Ces films, de quelques microns d’épaisseur, améliorent la résistance à l’érosion provoquée par la pluie, le sable ou la grêle. Sur un hélicoptère militaire déployé en environnement désertique, la perte de masse sur une pale non protégée peut atteindre 20 grammes par vol.
L’assemblage entre les matériaux composites et les parties métalliques reste un point de fragilité. Les jonctions par adhésifs, les fixations mécaniques hybrides et les traitements de surface (anodisation, électropolissage) sont des axes de travail essentiels pour limiter la création de fissures à ces interfaces.
Enfin, la tendance va vers la fabrication additive métallique (impression 3D) pour les moyeux ou éléments secondaires, permettant des géométries complexes avec une résistance optimisée. Des tests sur des pièces en Inconel 718 imprimées ont démontré une durée de vie multipliée par 2 par rapport aux pièces usinées conventionnelles.
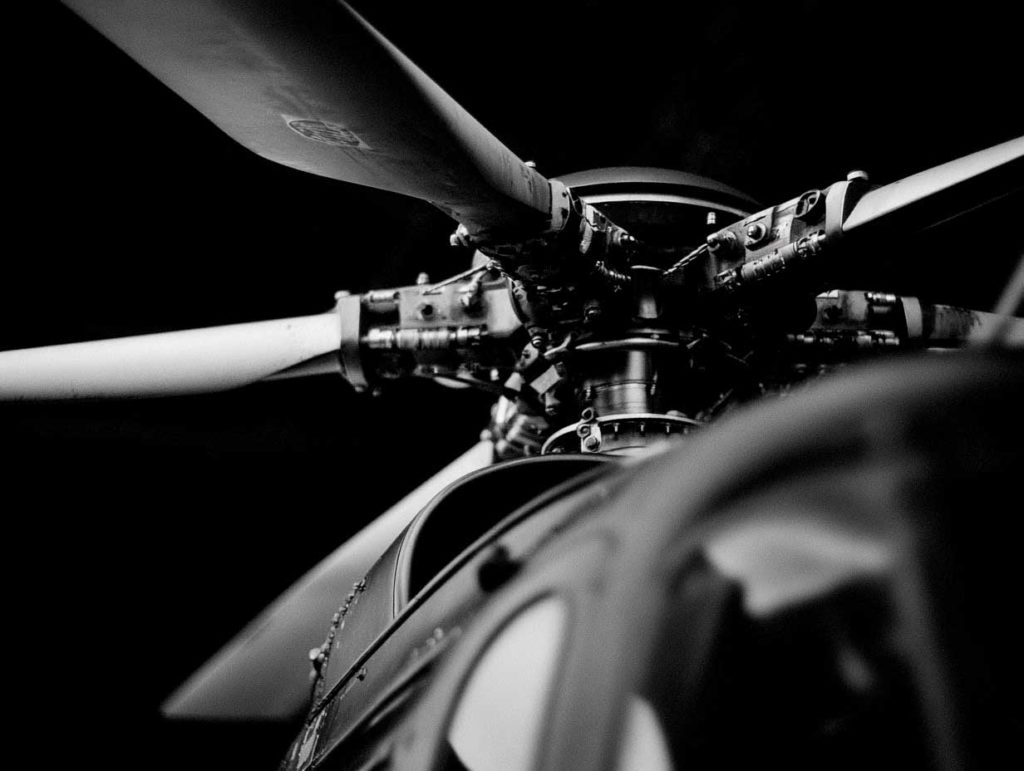
Une surveillance active des contraintes et de la fatigue en temps réel
Prolonger la durée de vie des rotors principaux sans compromettre la sécurité passe par une meilleure connaissance de leur état réel en vol. Le développement de systèmes de surveillance intégrés permet de remplacer le cycle de maintenance à intervalles fixes par une logique de maintenance conditionnelle.
Les rotors de dernière génération intègrent des capteurs piézoélectriques, accéléromètres et extensomètres directement dans les pales ou dans les têtes rotor. Ces capteurs mesurent en continu les vibrations, la température, la charge appliquée et les micro-déformations. Les données sont analysées par des algorithmes embarqués ou transmises en temps réel à des centres de maintenance.
Le système IVHM (Integrated Vehicle Health Management) développé par Sikorsky, ou le module Helionix d’Airbus Helicopters, sont des exemples de ces architectures. Elles permettent d’anticiper l’apparition de dommages avant qu’ils ne deviennent critiques, d’adapter les intervalles de maintenance, et de limiter les inspections inutiles.
Sur certains modèles comme le Bell 429, la surveillance des pales permet de détecter un défaut de balourd supérieur à 20 grammes ou une variation d’amplitude vibratoire de 0,1 g, indicateurs précoces de désalignement ou de fissure interne.
Les gains sont réels : selon Airbus, l’usage du monitoring actif permet de prolonger la durée de vie utile des pales de 15 à 25 %, soit plusieurs centaines d’heures de vol supplémentaires. Ce gain est d’autant plus significatif que le coût horaire d’exploitation d’un hélicoptère léger se situe entre 800 et 2000 euros, et jusqu’à 6000 euros pour un appareil lourd comme le H225M.
Une conception repensée pour réduire les efforts mécaniques
L’amélioration de la durée de vie des rotors principaux passe aussi par une conception plus intelligente, destinée à réduire les efforts mécaniques sur l’ensemble de la tête rotor. Plusieurs axes sont explorés par les constructeurs :
- La suppression des articulations mécaniques au profit de têtes rotor rigides ou semi-rigides, qui réduisent les zones de friction et d’usure. Ces têtes utilisent la flexibilité des matériaux pour absorber les mouvements, à la place des pivots classiques. Le S-97 Raider de Sikorsky utilise cette approche pour des vitesses de vol plus élevées avec moins d’entretien.
- L’optimisation aérodynamique des profils de pales permet de limiter les zones de pression critique et d’équilibrer la portance. Des pales asymétriques, à flèche inversée ou à géométrie variable, sont testées pour réduire les amplitudes vibratoires et allonger les cycles de vie.
- La réduction de l’entraînement parasite, notamment en diminuant les frottements dans les transmissions et les engrenages liés au rotor principal. Sur le NH90, les ingénieurs de NHIndustries ont retravaillé la cinématique de la boîte de transmission pour réduire la dissipation thermique et limiter les pics de couple en rotation.
- Enfin, des travaux sont menés sur l’amortissement dynamique des têtes rotor, par l’ajout de masses mobiles ou de systèmes électromagnétiques capables d’absorber les vibrations mécaniques selon leur fréquence. Ces solutions actives permettent d’atténuer les phénomènes de résonance à certaines vitesses critiques.
L’enjeu, dans tous ces cas, est de diminuer les charges alternées et la fatigue mécanique globale du système rotor, en maintenant un haut niveau de performance et de sécurité.
Un enjeu économique stratégique pour les opérateurs
Allonger la durée de vie des rotors principaux n’est pas qu’un objectif technique. C’est un facteur de rentabilité directe pour les exploitants. Sur un hélicoptère civil de 5 tonnes, les frais liés au rotor principal (entretien, remplacement, inspection) peuvent représenter jusqu’à 30 % du coût total de possession.
Un allongement de 10 % de la durée de vie certifiée d’un rotor principal se traduit par un gain direct de plusieurs centaines de milliers d’euros sur le cycle de vie de l’appareil. Pour les flottes militaires, l’impact est encore plus significatif : sur les NH90 français, la réduction des cycles de maintenance du rotor principal est l’un des objectifs prioritaires du plan MCO (Maintien en Condition Opérationnelle).
Le développement de rotors plus durables permet également de limiter la dépendance aux fournisseurs, de réduire les stocks de rechange, et d’améliorer la disponibilité opérationnelle des hélicoptères. Ce facteur devient stratégique en contexte de guerre ou de déploiement en zone isolée.
Mais ces gains ne sont pas automatiques. Ils nécessitent des investissements lourds en R\&D, en qualification et en certification. Le moindre changement de matériau ou de conception sur une pale rotor doit être validé par des essais mécaniques, des simulations de charge et des tests en vol, souvent étalés sur plus de 18 mois.
Il ne s’agit donc pas d’innovation rapide, mais de progrès par paliers successifs, validés par la fiabilité, la sécurité et le coût.
HELICOLAND est le spécialiste de l’hélicoptère